- 数字化大屏
在智能制造浪潮下,工厂指挥中心的巨型屏幕已成为企业数字化转型的标志性符号。这些屏幕以动态图表、实时数据流和多媒体交互,直观呈现生产、设备、物流等核心运营指标。然而,当企业投入重金打造“数字化窗口”时,更需思考:如何让这些屏幕从“视觉符号”蜕变为驱动管理变革的“价值中枢”?
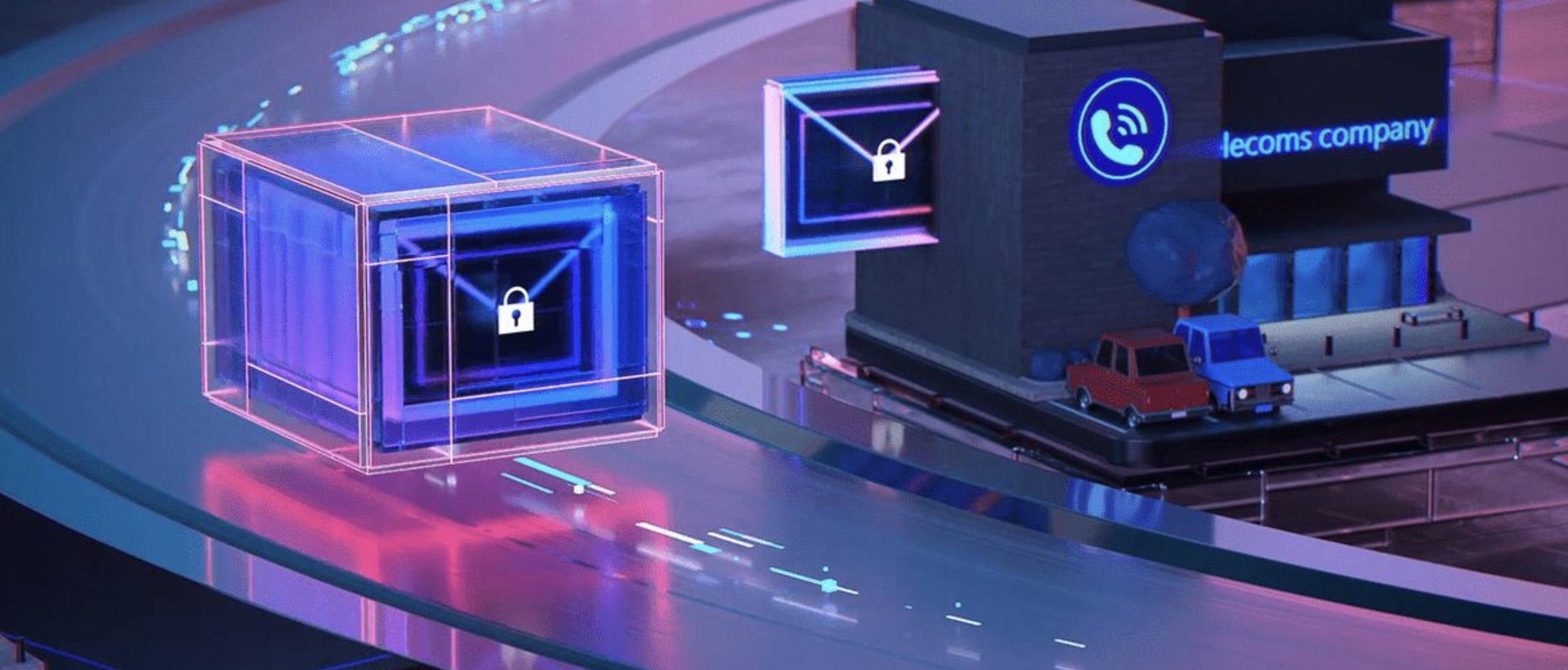
一、表层价值:从“面子工程”到“数字名片”的认知突破
多数企业启动数字化大屏项目的初衷,往往聚焦于“品牌展示”与“形象升级”:
- 客户考察与政府接待
通过动态数据看板,快速传递“智能制造”的技术实力; - 内部激励与文化渗透
结合数据动画与多媒体素材,增强员工对数字化转型的认同感。
但若仅停留于“视觉震撼”,大屏极易沦为“数字花瓶”。真正的价值跃迁,需将其从“展示工具”升级为“管理平台”,实现从“看得见”到“用得上”的跨越。
二、深层价值:构建“数据-决策-行动”的闭环生态
数字化大屏的核心使命,是成为贯通工厂运营的“神经中枢”,其价值体现在三大维度:
1. 数据穿透:从宏观到微观的精准洞察
- 多级钻取能力
支持从工厂级到设备级的逐层下钻(如:点击“车间A”→查看“产线3”→定位“设备07”→调取班次运行参数); - 实时数据刷新
依托MES、SCADA等系统,实现生产、能耗、质量数据的秒级同步,杜绝“数据滞后”导致的决策误判。
2. 目标管理:从指标展示到绩效驱动
- KPI可视化
将产量达标率、设备OEE、质量合格率等核心指标与目标值动态对比,偏差值以红黄灯预警; - 问题闭环追踪
针对异常指标,自动生成改进任务清单(如:设备故障预警→关联8D报告→跟踪PDCA闭环)。
3. 协同透明:从信息孤岛到全员改善
- 跨部门协同
基于统一数据平台,生产、质量、设备部门可实时同步问题进展(如:设备异常导致停机→同步显示维修进度与生产调整方案); - 文化渗透
通过“问题曝光台”“改进案例榜”等模块,营造“人人关注数据、人人参与改善”的氛围。
三、价值验证:三步识别“真伪大屏”
当企业面对“大屏是否沦为摆设”的质疑时,可通过以下方法检验:
- 数据穿透测试
要求演示者从大屏指标逐层下钻至设备级数据,若无法查看单台设备实时参数,则说明系统未与现场数据深度打通; - 行动闭环验证
检查大屏是否关联改进任务(如:偏差分析报告、责任人清单、改进进度跟踪),若无配套行动,则数据仅具“观赏性”; - 日常使用评估
观察大屏是否融入日常管理(如:晨会基于大屏数据复盘、班组根据预警启动应急响应),若仅在接待时启用,则系统已陷入“数据孤岛”。
四、长效运营:让大屏成为“持续改善”的引擎
为避免大屏沦为“一次性工程”,需构建“数据-改进-迭代”的闭环:
- 月度数据复盘
以大屏指标为基准,召开跨部门改进会议,分析KPI达成率与改进措施效果; - PDCA动态追踪
对偏差问题实施5WHY根因分析,任务状态实时更新于大屏(如:问题原因→改进措施→效果验证); - 知识沉淀共享
将优秀改进案例通过大屏和知识库推广,推动跨车间经验复制。
五、落地路径:从规划到执行的五步法
- 需求导向设计
明确核心用户(如车间主任、设备工程师)的使用场景,优先开发“高频刚需”模块(如:设备故障预警、生产进度追踪); - 试点先行验证
选取1-2个关键车间试点,完成数据采集、分析、改进的闭环验证后,再逐步推广; - 数据中台支撑
构建统一数据平台,整合MES、ERP、IoT数据,实现跨系统指标实时计算; - 运维机制保障
设立专职大屏管理员,负责数据接口维护、看板优化与用户培训; - 持续迭代升级
建立用户反馈机制,定期优化界面交互与内容布局(如:按季节调整数据看板优先级)。
数字化大屏的价值,不在于屏幕尺寸或视觉效果,而在于能否将数据转化为决策力、将指标转化为行动力、将展示转化为生产力。唯有打通从数据采集到行动闭环的全链条,让大屏成为“日常管理工具”而非“参观接待道具”,才能真正释放数字化转型的效能红利,推动制造企业迈向精益运营的新高度。